Exploring the World of 3D Printing on Fabric
3D printing isn’t just for tech gadgets, replacement parts or figurines anymore—it’s also making waves in the fashion world. Imagine being able to print intricate custom designs and incorporate it directly in the fabric of a garment. Now stop imagining because it’s already happening, and it’s pretty amazing!
How Does It Work?
3D printing on fabric combines the world of fashion and technology through digital innovation in textile design. For centuries, the best way to create 3 dimensional texture on a textile surface was embroidery, but now designers can use a 3D printer to layer material (like plastic filament or even flexible rubber) onto fabric. The result? Unique, textured patterns using materials that wouldn’t be possible with traditional techniques, Not to mention the hours of time it saves!
First things first, you need to figure out what your brand values are. What do you stand for? Are you all about sustainability, inclusivity, or pushing boundaries with innovative design? Once you’ve nailed down your values, it’s time to think about how you want to communicate them.
This brings us to your brand voice and tone. Are you fun and playful, serious and sophisticated, or somewhere in between? Your brand voice is how you speak to your audience – the language you use, the emotions you evoke. Your tone is the specific way you express that voice in different situations, whether it’s a cheeky Instagram post or a heartfelt brand manifesto.
Why It’s Cool
- Customization: You can create one-of-a-kind designs that are tailored to your vision, whether it’s for fashion, interior design, or art.
- Textures & Layers: 3D printing adds a whole new dimension to fabric—literally. Think bold patterns, raised textures, and even wearable structures that move with the
- Sustainability: Since 3D printers use only the material you need, there’s less waste compared to traditional fabric manufacturing methods.
Real-World Examples
Designers are already pushing the boundaries of what 3D printing can do. For example, Iris van Herpen, a Dutch fashion designer known for her
cutting-edge designs, has created stunning runway-ready dresses using 3D-printed elements. Her work explores the intersection of technology, fashion, and nature, pushing the envelope of what’s possible in garment design.
In the world of eco-friendly fashion, designers are creating 3D-printed fabrics from recycled plastics or organic materials, reducing waste while still producing high-end, innovative designs. Stella McCartney has even experimented with 3D-printed shoes as part of her sustainability initiative, offering a glimpse of a greener future in fashion.
3D-printed fabrics are also finding their way into home décor and accessories. From upholstered chairs with custom patterns to 3D-printed bags and shoes, designers are integrating this technology into a broad range of consumer products.
On the other end of the spectrum, we have Chanel. The epitome of timeless elegance and luxury, Chanel’s brand identity exudes sophistication and class. From the interlocking Cs to the signature quilted handbags, everything about Chanel screams luxury and refinement.
And let’s not forget about Supreme. The streetwear brand has built a cult following around its brand identity of exclusivity, coolness, and counterculture. The red-and-white logo has become a status symbol, sparking hype and demand with every new drop.
Not to pat ourselves on the back, but this past fashion week we had multiple students and alumni showcase and embrace their brand identity. Let’s take a peak…
The Future of 3D Printing on Fabric
As 3D printing technology advances, expect even more possibilities. Faster printing, a wider range of materials, and even more stunning designs are on the horizon. Some innovations on the way include:
On the other end of the spectrum, we have Chanel. The epitome of timeless elegance and luxury, Chanel’s brand identity exudes sophistication and class. From the interlocking Cs to the signature quilted handbags, everything about Chanel screams luxury and refinement.
And let’s not forget about Supreme. The streetwear brand has built a cult following around its brand identity of exclusivity, coolness, and counterculture. The red-and-white logo has become a status symbol, sparking hype and demand with every new drop.
Not to pat ourselves on the back, but this past fashion week we had multiple students and alumni showcase and embrace their brand identity. Let’s take a peak…
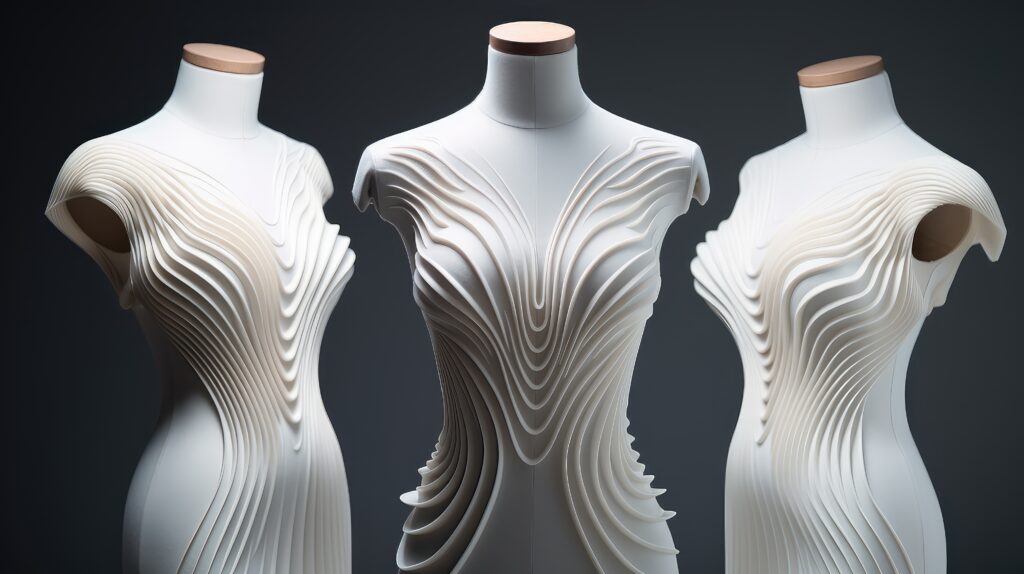
Smart fabrics: 3D printing could lead to fabrics that respond to environmental changes—like temperature-sensitive textiles or fabrics that change shape or color based on movement.
On-demand manufacturing: Instead of mass production, 3D printing could make it possible to print garments and accessories on demand, reducing overproduction and waste in the fashion industry.
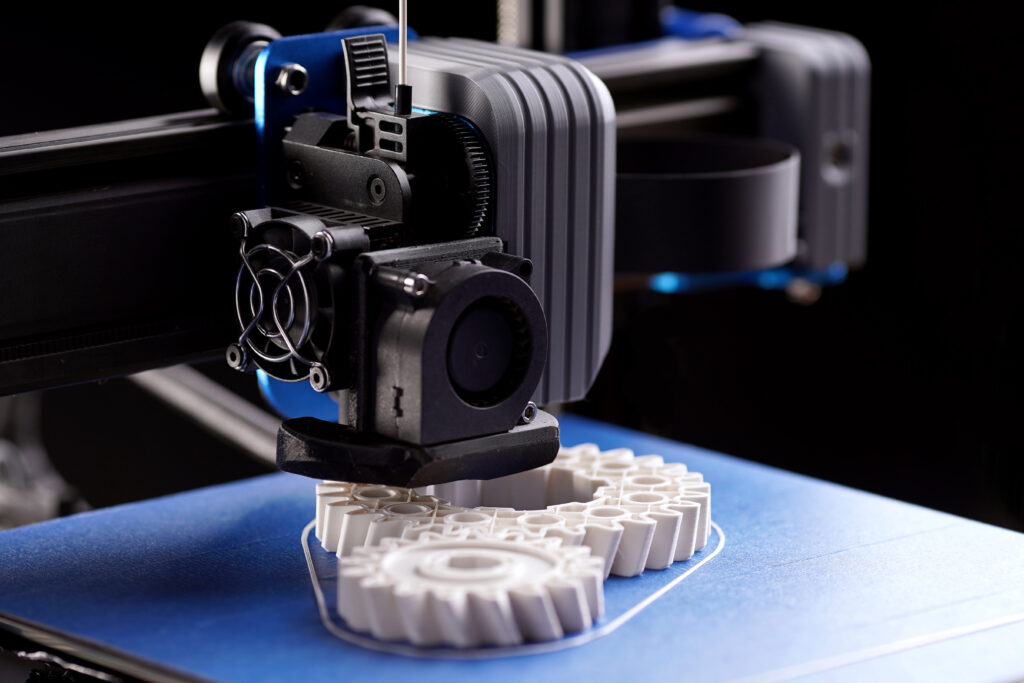
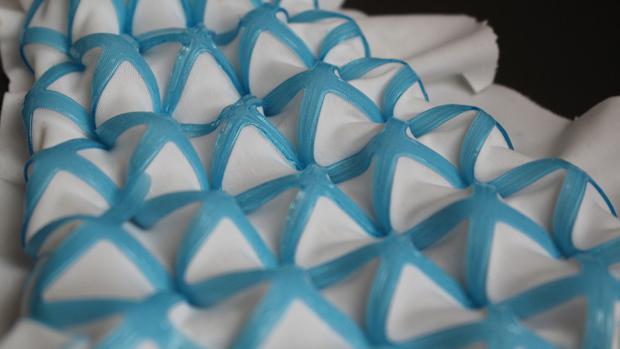
Hybrid textiles: Combining traditional fabrics with 3D-printed elements, like creating a base garment made from natural fibers and adding 3D-printed embellishments or structural pieces.
Whether you’re a fashionista or just love seeing innovation in action, 3D printing on fabric is definitely something to watch! It’s transforming how we think about design, materials, and the very process of creating fashion and textiles. The future is not only digital—it’s 3D.